Are you thinking about buying a MIG welder and want to make the best choice? One size does not fit all with MIG welders. This article will help you to choose the right MIG welder and the most important features to consider for your specific application.
What Type of MIG Welder Is Best for You?
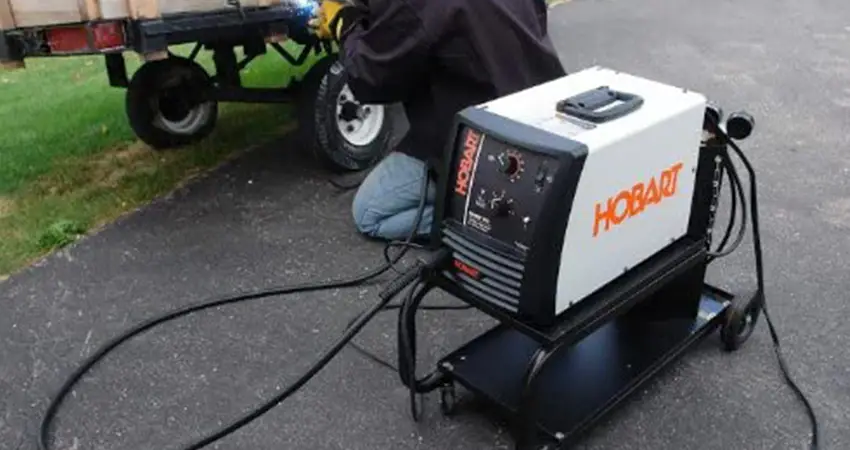
The 2 Basic Types of MIG Welders
- Gas Metal Arc Welding (GMAW): This type uses inert gas to protect the arc and molten weld puddle. Depending on different metal types, you can equip the welder with a bottle of argon, CO2 or a combination of 75% argon and 25% CO2. Helium can also be used in certain applications.
- Flux-Cored Arc Welding (FCAW): This type of MIG welding used flux-cored electrode wire to produce gas shielding around the weld puddle. The flux inside the electrode wire vaporizes in the weld arc and produces an inert gas shield around the weld as it burns off.
Most MIG welders are capable of both flux-cored and gas-shielded welding. For flux-cored MIG you just need wire that matches the metals you’re welding. For inert gas MIG, you need a gas cylinder charged with the right inert gas, a gas regulator, hoses, solenoid and gas gun tip.
Pros and Cons of Gas MIG welding (GMAW)
PROS of gas MIG welding:
- Cleaner welding process with less smoke and splatter (better for indoors use)
- Easier to see the weld puddle, making weld accuracy and quality easier to achieve for inexperienced welders
- Ability to weld a wider range of metals, such as aluminum, chrome alloys, etc.
- Ability to weld thin metals without burning through by simply turning down the voltage
CONS of gas MIG welding:
- More expensive — GMAW is roughly ___ as expensive as FCAW due to more equipment and consumable costs
- Heavier and less mobile — with gas MIG you need a gas cylinder, regulator and hoses, plus a cart to contain and move it around. This makes it much heavier and harder to transport.
- More complex — there are more elements to get right to create quality welds, which means more education and practice is needed
- Doesn’t work outside in the wind because the shielding gas blows away
Pros and Cons of Flux-Cored MIG Welding (FCAW)
PROS of flux-cored MIG welding:
- Cheaper — about ____ the cost of GMAW
- More mobile — you can take a flux-cored welder anywhere that has an adequate power source
- Simpler to set up and learn to create good quality welds
- Flux-core welding creates stronger welds on a more consistent basis if you’re a beginner — even if your settings are off a bit or your work piece isn’t properly cleaned the expanding gas cloud will clean up the weld area so you get more penetration
- Works better than inert gas MIG outdoors (though not as good as a stick welder)
CONS of flux-cored MIG welding:
- Lots of smoke, fumes and spatter from the flux burning off obscure the weld pool — this makes it harder to see what you’re welding and keep a consistent line and distance from your target
- Welds tend to be more “ugly” because it’s harder to control your weld pool and direction
- “Dirty” welds — slag needs to be chipped off with a hammer and the area around the weld gets smoky burn marks that require wire brushing to clean up
- Flux-cored wire is about twice as expensive as metal-only wire
- Doesn’t work well with aluminum or some alloys, since the burning flux can cause oxidation
- Doesn’t work well with thin metals, as the burning flux generates high localized heat which leads to burn-through and warping of the base metal
Flux-Cored MIG vs. Gas MIG for Different Situations
Intended Use | Flux-Cored MIG | Gas MIG |
Auto Body | Poor | Best |
Auto Frame / Bumper | Good | Best |
Trailer repair (outdoors) | Best | Good |
Sheet Metal | Poor | Best |
Tubing | Good | Best |
Roll Cages | Good | Best |
Fence building | Best | Good |
Heavy pipe | Best | Good |
Farm equipment (outdoors) | Good | Poor |
Iron art | Best | Good |
Detailed projects | Poor | Best |
Bicycle repair | Poor | Best |
Aluminum boat repair | Poor | Good |
Iron | Best | Good |
Carbon steel | Best | Best |
Aluminum | Poor | Good |
Bronze | Poor | Good |
Chrome moly | Good | Best |
Stainless steel | Good | Best |
Copper | Poor | Good |
Magnesium | Poor | Good |
Nickel | Poor | Good |
MIG Welding Transfer Modes
In addition to the MIG welder type, you can choose between five different MIG transfer mode technologies used to melt and transfer metal from the electrode to the weld. Each transfer mode has its strengths and weaknesses, and you want to consider your intended uses before making your choice.
- Short Circuit Transfer Mode: This mode uses low-voltage current to melt and join the base and electrode metals. The electrode wire is rapidly extended between 20-200 times per second, making physical contact with the base metal to enable the transfer. It does not require advanced electronics to control the weld arc. Short circuit transfer with carbon steel generally uses 75% argon/25% CO2 shielding gas.
PROS: Short Circuit Transfer Mode It works on all welding positions. It can weld everything from thin sheet metal to thick plate and pipes. It can be used with stainless steel. Low voltage is needed with Short Circuit Transfer so this mode is ideal for low-amperage 110V hobby welders and smaller 220V mobile welders up to 180 amps.
CONS: Short Circuit Transfer Mode is sensitive to the distance between the gun tip and base metal — too close and the electrode breaks off and causes splatter, too far and you lose contact creating gaps in the weld. It ony works with gas-shielded MIG (GMAW) using metal wire.
VERDICT: Short Circuit Transfer Mode is best for low-voltage welders. - Globular Transfer Mode: This mode uses high-voltage current and melts the electrode metal into globs to join them with the base metal. The drops are larger in diameter than the electrode wire. Gravity is used to feed the drops into the weld puddle. Globular transfer requires 100% CO2 shielding gas.
PROS: Works with both flux-cored MIG (FCAW) and gas MIG (GMAW).
CONS: Globular Transfer Mode does not work well for vertical and overhead welds, and it tends to create a lot of splatter and bumpy-looking welds. It only works with carbon steel, since the 100% CO2 gas causes oxidation of aluminum and other types of alloys.
VERDICT: Globular Transfer Mode is best for manufacturing applications requiring heavy horizontal welds where weld appearance is not a major factor, and there is a strong power source available to generate the high amperage required. - Spray Transfer Mode: This MIG transfer mode uses high voltage current and melts the electrode into fine droplets and transfers it to the base metal. It requires a high wire speed and high amperage to work properly. It creates a big weld puddle, which makes it ideal for thicker metals. Spray transfer works with both carbon and stainless steel and requires at least 80% argon shielding gas.
PROS: Spray Transfer Mode works well for thicker metals where deep / wide penetration is required. It produces very little spatter. Works with stainless steel.
CONS: It doesn’t work well on vertical or overhead welds. It consumes a lot of electrode wire creating a large weld puddle.
VERDICT: Spray Transfer Mode is best for horizontal welds on thick material (especially stainless steel) where a large weld puddle is needed, and there is a strong power source available to generate high amperage. The ideal application is manufacturing. - Pulsed Spray Transfer Mode: This mode also uses high-voltage current and melts the electrode wire into fine droplets. It alternates between spray transfer mode and and lower voltage “cooling” mode. Pulsed spray transfer can weld both carbon steel and stainless steel and requires at least 80% argon shielding gas.
PROS: Pulsed Spray Transfer Mode can weld thinner materials (due to the cooling cycle) and thick plate, and works well on vertical and overhead welds.
CONS: It requires high concentrations of argon shielding gas, which makes it more expensive.
VERDICT: Pulsed Spray Transfer Mode combines the benefits of Spray Transfer Mode with the ability to weld in vertical and overhead positions. It’s an excellent choice to create consistent, good-looking welds with deep penetration. - Surface Tension Transfer (STT) Mode: According to Lincoln Electric’s STT documentation STT is a transfer mode patented by and used in Lincoln Electric MIG welders. Basically, it creates a molten glob of metal at the tip of the electrode wire which shorts when it touches the weld puddle. At the point the short occurs, the voltage is reduced and modulated to let the metal flow into the puddle, then as the short ends the voltage is cut to prevent splatter.
PROS: Surface Tension Transfer Mode can be used for a wide variety of metals, in all welding positions, is faster to learn and generates better quality welds with less splatter and smoke.
CONS: This is a premium feature on Lincoln Electric welders only, so it costs more.
VERDICT: Surface Tension Transfer Mode is a modern version of Globular Transfer Mode that helps create a consistent weld and excellent penetration without splatter. It uses advanced electronics to increase consistency and ease of welding.
Important MIG Welder Features to Consider
Multipurpose or Single Purpose Machine?
If you’re planning on welding different types of metal, thicknesses and designs, you should consider getting a multipurpose MIG / TIG / stick welder. This is especially true if you have limited shop space for multiple machines, or will be traveling and welding on site.
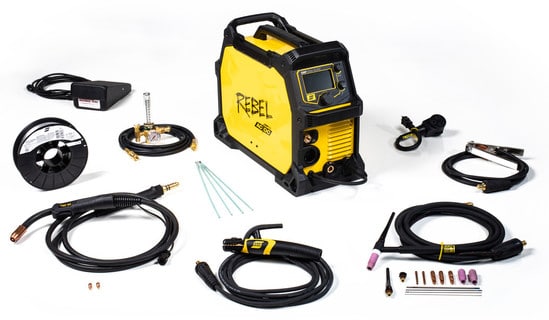
Top quality multipurpose welding machines come with most everything you need to do:
- Stick / arc welding (SMAW)
- Inert gase MIG (GMAW)
- Flux-core MIG (FCAW)
- AC TIG (GTAW-AC)
- DC TIG (GTAW-DC)
- Pulsed TIG (GTAW-P)
PROS of multipurpose welders: A multipurpose machine will allow you to do the highest quality welds with the right technology and consumables from a single machine. You can swap out between different jobs like TIG welding aluminum, to MIG welding a steel chair frame, to stick welding heavy farm equipment. One purchase gets you everything in a transportable package that takes up far less space than multiple welding machines.
CONS of multipurpose welders: The downsides of a multipurpose MIG / TIG / stick setup is the high cost, greater complexity and need to learn more than one welding method. Unless you do lots of different jobs and need a single machine due to space constraints, a multipurpose machine is probably overkill for you.
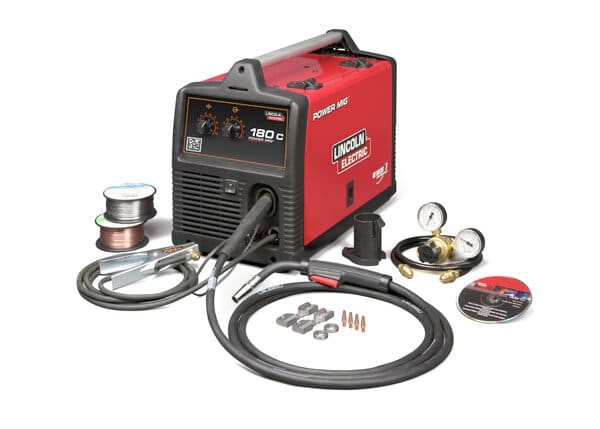
In comparison, a single purpose MIG welder (or dual flux-core MIG / inert gas MIG) is a simpler and less costly option suitable for a narrower range of welding jobs.
PROS of single purpose MIG welders: A single purpose MIG welder will be substantially cheaper and fully adequate for most steel welding jobs. You only need to perfect one welding method with one set of accessories and consumables. This makes everything a lot simpler.
CONS of single purpose MIG welders: Buying a single purpose MIG welder (or dual flux-core MIG / inert gas MIG) will limit you in two key areas: 1) welding alternate materials like thin aluminum, bronze or titanium (ideal for TIG welders), and 2) welding outdoors on heavy farm equipment, pipe or plate (ideal for stick arc welders).
Voltage and Amperage
The voltage is the power your welder draws from the power source outlet, and the amperage is the power it outputs to your work piece.
110 Volt MIG Welders
If you’re working with small DIY projects or amateur home repair jobs, you don’t plan to weld anything thicker than 1/8 inch and don’t weld for extended periods of time, then a small 110V MIG machine is sufficient. Most 110V MIG welders are only rated to a maximum of 80-100 amps and have a low duty cycle (30% or lower – see below). That means they can only generate enough heat to weld thin metal for short periods.
220 Volt MIG Welders
If you’re planning on working with bigger projects or doing professional jobs, you need to get a 220V machine. 220V MIG welders generally output anywhere from 20-220 amps. Above 200 amps you can MIG weld up to 1/2 inch plate, and comfortably weld 1/4 inch plate and pipes. 220 volt MIG welders can also be turned down to weld thin metals. 220V is the best overall option.
Dual Voltage MIG Welders
You can also get a dual voltage mig welder that can work with both 110/220 volts. This allows you to use alternate input power sources — a 110V garage plug for light duty work, and a 220V plug or generator for heavy duty work.
MIG Wire Spool Size
The wire spool size is very important and needs to be matched to the type of work and expected duration of your welds. The table below shows the different spool sizes with metal wire capacity by common diameters and metal type.
Spool Size | Wire Size | Wire Capacity |
4 inch | 0.025 – 0.045 inch | 1 to 2 pounds carbon steel 2 pounds stainless steel 1 pound aluminum |
8 inch | 0.025 – 0.045 inch | 11 to 12 pounds carbon steel 10 to 12 pounds stainless steel 8 to 10 pounds aluminum |
12 inch | 0.025 – 0.045 inch | 33 to 45 pounds carbon steel 25 to 33 pounds stainless steel 16 to 20 pounds aluminum |
24 inch | 0.025 – 0.0875 inch | 150 to 165 pounds carbon steel |
The size of MIG wire spool you choose should match the amount and type of wire you need for the job.
Most small-to-midsize MIG welders use 4 inch or 8 inch spools. These are appropriate for smaller jobs and shorter weld times. A small 4 inch spool won’t feed as smoothly as a larger spool, and you will need to change it often if you weld a lot, so keep this in mind. An 8 inch spool is fine for most types of MIG welding work.
The larger spool sizes 12 and 24 inch are used for continuous welding operations such as manufacturing, iron work construction, ship building and pipes. These spools are designed for large, high amperage MIG welders.
If you’re investing in a Spray Transfer Mode MIG machine you should go with a larger spool size, since these welders create a large weld pool and consume more wire per foot of weld than other transfer modes.
For MIG welding aluminum a lot you should choose larger spool sizes (8 or 12 inches). Aluminum wire tends to not feed off a small spool smoothly, which can negatively affect the your weld quality. A larger spool will help prevent “rat tails” in the feed mechanism.
Duty Cycle
Loosely defined, the duty cycle of a welding machine is the percentage of a 10 minute period in which it can weld at full arc capacity without losing amperage and overheating.
A 100% duty cycle welder means it can weld continuously for a full 10 minutes without pausing.
If the duty cycle is 30%, it will weld continuously for 3 minutes out of 10 minutes.
With a 20% duty cycle, you can MIG weld continuously for only 2 of the 10 minutes.
Once a MIG welder reaches its maximum duty cyle it has to cool down for a while, or it will overheat. This means you cannot continue working until the machine is ready again. In a continuous production environment like manufacturing, pipe laying or high rise construction having a high duty cycle is critical. For a small garage welder it may not matter much.
The rule of thumb here is, the higher the price, the better the welder in terms of the duty cycle. When in doubt, invest in a MIG welder with the highest duty cycle you can afford for the amperage you need.
Controls and Electronics
MIG welding electronics have advanced greatly in the last 20 years. Today, most mid-level MIG welders have microcircuits and control software that facilitates smooth welding, control of the weld puddle and avoidance of short circuits and splatter. That’s why MIG is the easiest to learn and become productive with of all the welding methods.
Generally speaking, you want fine controls for wire speed, voltage and wire feed tension. Higher quality welders run smoother and allow finer adjustments than cheap welders.
The variable dials for both the wire feed speed and voltage control should be easy to read, clearly marked and easy to adjust with infinite (not stepped) adjustments. A digital readout is very helpful to see the actual settings of the machine. This will let you turn down the amps and wire speed for thin sheet metal and detail work, while turning it up for thicker materials.
Weight and Mobility
If you’re working in a welding shop where you don’t have to move the welder too often, you can go with a bulky MIG welder. But if you’re planning on moving it around, you must go for a smaller and compact welder.
A heavy MIG machine with large gas cylinders will require a large cart to secure it and move around. This significantly affects your mobility around the shop, and hinders your ability to travel to weld sites.
If you plan to travel and weld onsite often (outside of your garage or shop), then it’s wise to set up your MIG welder for flux-cored welding. Eliminating the gas cylinder, extra hoses, regulator and cart will make your welder much lighter and much more mobile. The downside is losing the cleanliness and control of inert gas shielding, but flux-cored MIG does a good job of producing strong welds with good penetration, particularly outdoors.
Gas Regulator
A gas regulator indicates the pressure of the gas and the remaining gas inside the cylinder. Most gas MIG welders come with a good quality gas regulator included.
The connection between the gas regulator and gas cylinder is critical. If the seal is worn out or threads are stripped, you will lose gas and potentially introduce air into the mixture. This will cost you money and could impact your weld quality without you knowing why.
Some industrial-level MIG welders are set up with two gas bottles (argon or helium and CO2). A dual-gauge gas regulator / mixing valve can be used to create your own gas mixture. This is an advanced setup that requires a very accurate regulator, and shouldn’t be needed for the majority of MIG welding.
Making the Right MIG Welder Choice
Choosing the right MIG welder takes in a lot of considerations, as you can see above in the buying guide.
The rule of thumb is to buy the highest quality MIG welder that fits all the jobs you plan to do, can handle the different metals you work on, and has a high duty cycle.
We hope this gave you some good tips on how to choose a MIG welder and best of luck with your purchase!