MIG welders are widely used because of their versatility. You can use a MIG machine for welding just about any type of metal with minimal hassle and mess. It makes strong welds that have an aesthetically pleasing look when done right.
MIG welders have 5 key advantages over other welding methods.
Read on to learn more…
Advantage #1 MIG Welders Are Fast
With a MIG welder you just turn on the gas, power on the machine, make sure you’ve got a good ground and your surface is prepped, and start welding. There is literally no other setup. The gun is self-contained and ready to weld at any time.
With good-sized gas tank and a full spool of wire, you can usually weld for substantial distances before a MIG machine loses efficiency. After a short cool off period, you can quickly resume. This is important for production welding where continuous fast work is essential. It is also important for large pieces with long joint surfaces — it’s easier to remain consistent if you don’t have to start and stop frequently.
With stick welding you need to change the electrodes often, which slows down the welding.
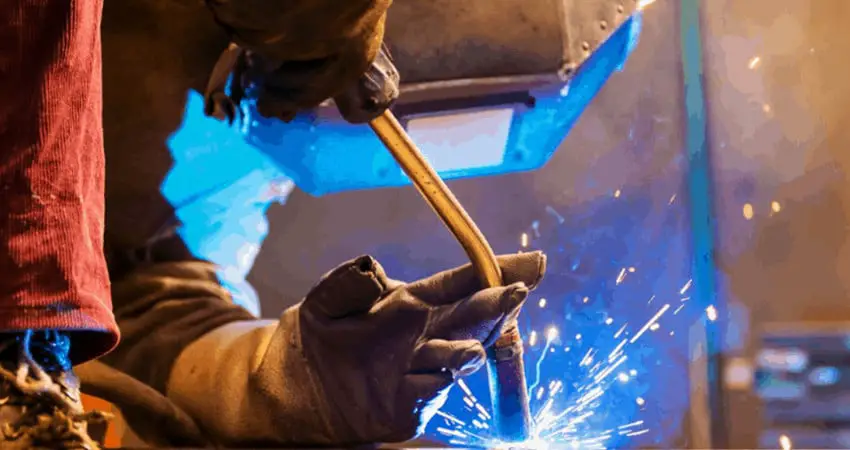
Advantage #2 Clean and Aesthetically Pleasing Welds
Regardless of the type of MIG welder, you will get cleaner welds than a stick welder is capable of. It produces less smoke, spatter and slag, allowing you to focus on the weld puddle and pattern. This means a MIG welder is inherently more capable of aesthetically pleasing welds.
The real benefit of clean welds is you don’t need to clean the area surrounding your weld joint. This may not matter when welding pipes or farm equipment. But it matters a lot when doing production welding, or working on a metal table or race car roll cage. A clean spatter-free weld area means you don’t have to spend hours with disc sander cleaning up after MIG welding.
The only time a MIG welder generally gets messy is when using flux core wire in windy conditions.
Advantage #3 MIG Welders Have More Adjustability
Today’s MIG welders have a wide array of settings that let you weld anything from thin sheet metal to thick plate with the same wire and gun.
MIG welders let you control the wire speed and amps independently, giving you near-infinite adjustability.
A faster wire speed creates more spatter and less penetration and generates a taller weld. A slower speed produces less spatter and deep penetration that produces a flatter weld. This allows the user to optimize the machine and adjust out common MIG behaviors such as popping or weld stacking.
You can turn down the heat to weld a thin piece of sheet metal without blowing through, or ramp up the heat to drive deep into thick pieces and tight joints.
You simply can’t get this range of adjustability with a stick welding machine.
Advantage #4 Good for Production Welding
Due to their speed, reliability and long welding time, MIG welders are ideal for production welding standard steel structures. Everything from fences to truck chassis can be welded efficiently. The keys to production welding are:
- Speed
- Consistency
- Weld quality & cleanliness
- Low down time
- Low consumable costs
On all five counts, a MIG welder will generally outperform a stick welder. For several of these factors a MIG will also outperform a TIG welder, too.
Bottom line, MIG welding is ideal for production-line work.
Advantage #5 MIG Welders are Easy To Use
A beginner level welder can start welding with a MIG welder within 5 minutes. Of course, that does not mean the welds will be good, but ease of use and quick startup make practicing easy.
Modern MIG welders have clear standard settings for most types and thicknesses of material. Just look on the table for the thickness of your material, follow the standard settings and you’ve got reasonably decent welds to start. From there, with some instruction practice and settings refinement, it’s just a matter of time until you become an intermediate-level welder.
A stick welder is a much more rudimentary tool. Getting decent welds on a consistent basis through the smoke and spatter takes significant practice. It’s also not easy to clean up the welds, requiring a lot of disc sanding, which takes time, effort and money.
A TIG welder takes much more practice and skill than a MIG welder. The weld cleanliness and accuracy you can achieve with a TIG is top-notch. But it takes quite awhile to learn to manage the weld pool and manipulate the gas, filler rod, pedal and tungsten electrode.
MIG Performance Factors
You should consider the following performance factors when choosing a MIG welder for your situation.
Amperage and Duty Cycle
Which type of materials you can weld largely depend on the amperage and duty cycle. A MIG welder with high amperage and high duty cycle can weld thicker metal for a long time.
To get the best performance a MIG welder must be supplied with sufficient current from a correctly installed 50-amp NEMA outlet. The circuit must use 4-6 gauge wire and run through a 50-amp breaker for overload protection.
Input Voltage
The correct electric outlet gives a MIG welding machine the power inputs it needs to run consistently without overheating and short-circuiting. Both 220 volts and 110 volts are used for MIG welders. Many machines can run on both.
220 volts is typical for a medium-to-large welder. You need a more powerful 220 volt input for industrial work and heavy materials, such as roll cages, bumpers, truck frames, pipes and heavy plates.
110 volts is normal for a small garage or shop welder. A MIG welder with 110 volts suitable to hobby shops and household-related work like fence railings, fixing tools, etc.
MIG Gun Quality
The gun is designed to feed wire smoothly and consistently, while shielding the weld with a protective gas bubble. It’s essential for best results that the spool feeds smoothly. There should be no kinks, burrs or pinches in the wire feed mechanism or cord. If the wire becomes tangled or bunched up, or simply feeds inconsistently, it will significantly hamper your weld quality.
Managing Short-Circuits
MIG welders face a lot of electrical current and heat stress, both from the materials and the welder’s own behavior. Short-circuits are common at the point of weld contact, especially if the ground is poor. If the MIG welder can’t handle the short-circuiting effectively, it creates a burst of spatter that ruins the weld.
A good MIG welding machine modifies the electrical current effectively before a short-circuit occurs. This prevents spatter and porosity in the weld pool. The result is much more predictable high-quality welds.
Thermal Overload Protection
A high-amp MIG welding machine can become overheated after a long period of continuous welding. The build up of resistance in the machine causes excess heat overload, which weakens the current and makes the welder less efficient.
This excess overheating is handled by thermal overload protection in modern MIG welders. The machine will automatically give signals that it’s losing efficiency then turn off to protect itself. After a cool-down period of 3-10 minutes it is ready to weld again.