Though welding aluminum is less suitable in MIG welding machines than TIG welding, it can be done effectively if the right procedure is followed. MIG machines can effectively weld aluminum materials over 14 gauge.
You need the right filler wire and spool gun, shielding gas, power settings, wire feed speed, surface preparation and surface temperature to weld aluminum with a MIG welder.
How to Weld Aluminum With a MIG Welder
Here the steps to weld aluminum with a MIG welder. These steps are organized evenly to forward the process with balance.

Step 1: Measure Material Thickness
MIG welding is more effective on aluminum from 14 gauge (0.074 inch) and up. If the material is not thick enough, the excess heat produced by the MIG arc, combined with aluminum’s high thermal conductivity and low melting point can punch holes in the surrounding material. If you don’t know the thickness of aluminum pieces you’re about to weld, then use a thickness gauge to identify them.
Step 2: Choose the Right Gas
Pure Argon gas is needed to weld 6000 series aluminum with a MIG welder. As studies show, a mixture of CO2 and Argon gas can’t be used because of contamination issues. It is safe to keep the flow rate 20 to 30 cubic feet per hour.
5000 series aluminum alloy requires a helium and argon gas mixture. This reduces the formation of magnesium oxide in the weld.
Step 3: Use a Spool Gun With the Right Filler Wire
MIG welding aluminum is best done with a spool gun, rather than a standard MIG gun used with steel wire. Aluminum wire is much softer and more malleable than steel wire, and does not travel through the wire feed tube easily, leading to birds nests and poor quality welds. With a spool gun, the wire feeds only a few inches right from the gun, reducing the propensity for the wire to kink and tangle. It also helps to use a Teflon wire feed tube liner, rather than a steel one.
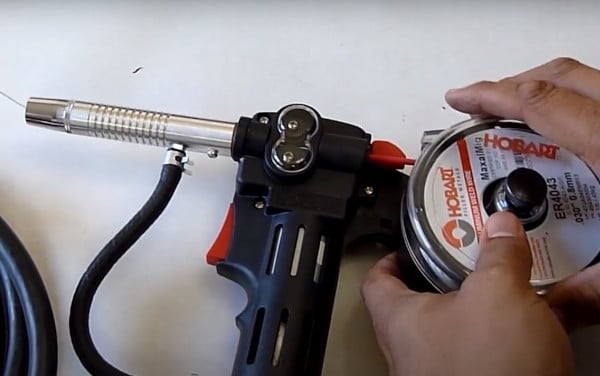
The filler wire you use for welding aluminum depends on the type of metal. It should match the melting point of the base metal pieces.
- For welding 6000 series aluminum a good filler wire is ER4043.
- For welding 5000 series aluminum alloys you should generally use ER5356.
Step 4: Optimize Your MIG Machine Settings for Aluminum
Your next step is to configure your MIG welder’s settings for welding aluminum as follows:

- Wire speed: Increase the wire speed to 1.5 to 2 times higher than the equivalent steel wire speed. You will need to move quickly while welding aluminum to avoid over-melting the work piece. A high wire speed ensures you get enough filler material into the weld puddle.
- Wire tension: Set the wire roller tension as low as possible but high enough to ensure smooth feeding. Basically, loosen it until the wire slips, then tighten it a bit so it feeds smoothly. This will help prevent wire deformation, kinking and bird nests.
- Voltage / amperage setting: Increase the power level to 1.5 times higher than that is required to a steel plate of similar thickness. You can look at your MIG welder’s voltage and wire speed chart and multiply the voltage setting by 1.5.
- Transfer method: MIG welding aluminum works best with pulse transfer or spray transfer methods. Pulse transfer works better on thin materials, while spray transfer works with thicker aluminum.
- Welding gun contact tip: If your welding gun contact tip is a standard steel one, then convert it to an aluminum oversize tip. The contact tip should be around 0.01 to 0.02 inch larger than the diameter of the filler wire. This will prevent overheated aluminum from expanding and jamming the tip.
Step 5: Remove All Oxidization From the Surface
Aluminum oxidizes very quickly. Oxidation will create brittle and porous welds, leading to failures. Before MIG welding aluminum you need clean the surface thoroughly of all oxidation with a clean stainless wire brush. If you don’t have a stainless brush, you can use clean sandpaper.
You generally want to brush in the same direction to sweep the oxides and hydrocarbons away. If you brush both ways it can embed the contaminants into the soft aluminum. Never use the same brush or sandpaper on both steel and aluminum, or you will introduce contamination into the area.
After brushing or sanding the area, clean it with acetone and a clean rag or paper towels. This eliminates any dust, grease or oil.
Step 6: Preheat the Welding Area
Preheating your work pieces can reduce the propensity for cracking due to rapid expansion / contraction. You can use a propane torch to preheat the weld area to around 200 degrees Farenheit (never above 230 F).
Adding a few tack welds at the ends of the piece and every couple inches can help preheat the aluminum, as well.
Safety Tips For MIG Welding Aluminum
Some important safety rules should be followed. According to research, MIG welding aluminum produces lots of heat, lots of harmful light and toxic gases.

- Wear a sealed welding helmet with side shields: This will protect you from over heat, sparks, UV radiation, nanoparticles and chemical burns.
- Wear a respirator: A sealed respirator that feeds fresh air into your helmet will protect you from toxic fumes and oxides that the aluminum welding process creates.
- Fire-resistant clothing: Aluminum welds are very hot, and can spray moten spatter. Proper gloves, jacket and pants will protect you from heat, spatter burns and radiation created in the aluminum welding process. Rubber-soled, steel toe capped safety shoes protect from electric shocks, heat, fire, burns and falling metal.
Related Questions
Is MIG or TIG Better For Welding Aluminum?
Both MIG (Metal Inert Gas) and TIG (Tungsten Inert Gas) can weld aluminum.

The MIG welding process is generally faster, but has less heat control, making it better for thicker aluminum and less-detailed work. MIG is easier to learn and is somewhat more mobile, as well.
TIG welding aluminum allows you to control the weld puddle and heat better than MIG. This makes TIG great for thin aluminum and aluminum alloys, and for creating quality welds on small work pieces. TIG machines are more suitable than MIG if the aluminum material is under 14 gauge.
Do You Need Gas to MIG Weld Aluminum?
Yes. Shielding gas is essential for MIG welding aluminum. You should use 100% argon gas for 6000 series aluminum, and helium/argon gas mixture for 5000 series aluminum alloys.
The shielding gas prevents oxygen and other gases from contaminating the weld. CO2 can’t be used in welding aluminum because of the reactivity.