“What kind of welder do I need?” is a very common question for people looking to buy a new welder. In this article, we describe the different types of welders and which ones match your requirements best.
Different Types of Welders and What They Do
Before deciding on the right welder for your situation, you need to know what the different types are and what they do. Here’s a quick summary:
MIG Welders
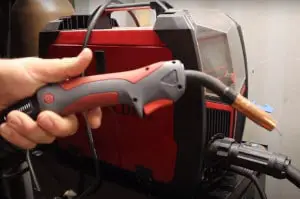
Gas Metal Arc MIG Welders (GMAW)
With gas metal arc MIG welding an electric arc is formed between the consumable solid wire electrode and the workpiece metal. The heat melts the electrode wire and the base metal. The electronic arc then transports the melted electrode wire into the weld joint and fuses it with the base metal puddle.
With this form of MIG welding gas from a cylinder (typically argon and CO2 mix for steel) flows through the welding gun to protect the molten weld puddle from the atmosphere so it does not oxidize or become contaminated.
The main benefits of gas MIG welding is ease of use, the ability to weld different types of metal effectively, and fast welding speed.
The main downsides of gas MIG are the general lack of portability and additional costs of the gas cylinders, regulator, lines and welding cart required.
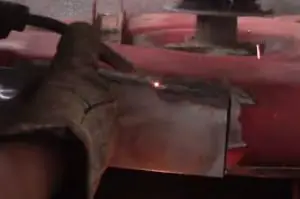
Flux-Cored Arc MIG Welders (FCAW)
With flux-cored arc MIG welding, the electrode wire is tubular with flux running through the center of the wire. Similar to GMAW MIG above, an electric arc is formed between the electrode wire and workpiece metal. The intense heat melts the electrode wire and the base metal. It also vaporizes the flux center, releasing inert gas that expands and protects the weld puddle from atmospheric contamination.
FCAW is very similar to SMAW (stick welding) below, except it uses a gun with automatic electrode feeding instead of a static consumable electrode stick.
The main benefits of flux-cored MIG welding are ease of use, welder portability, good weld penetration at low power levels, and fast welding speed.
The main downsides of flux-cored MIG are the additional cost of flux-cored wire, and the “dirty” welding process caused by smoke and slag from the flux core.
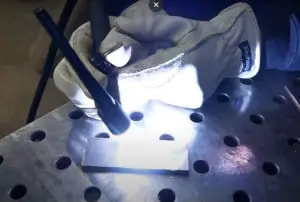
TIG Welders – Gas Tungsten Arc Welding (GTAW)
TIG (or GTAW) welding uses a small gun with inert gas shielding like gas MIG (GMAW) above. However, the welding arc forms between the base metal and a durable non-consumable tungsten electrode mounted in the gun. As the arc forms between the work piece and the tungsten tip, the welder feeds solid rod into the arc where it melts into a pool.
TIG welding generally uses argon or helium as the shielding gas to protect the weld from oxidation.
The main benefits of TIG welding are its ability to weld different types of metals effectively, and the ability to control the heat and weld pool very accurately, making welding very thin materials possible.
The main downsides of TIG welding are the high cost of TIG machines and the advanced training required to create quality TIG welds.
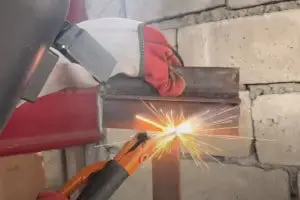
Stick Welders – Shielded Metal Arc Welding (SMAW)
Shielded metal arc (SMAW) is generally known as “stick welding”. As the arc forms between the electrode stick and the base metal it consumes the stick and the flux outer shell. When the flux vaporizes it produces intert shielding gas that protects the weld from atmospheric contamination, making it stronger.
Stick welding’s benefits include excellent weld penetration, ability to weld outdoors in the wind and rain, and the ability to weld poorly prepared or dirty metal together.
The main downsides of SMAW stick welding are that stick welding is slow since it requires changing sticks, and the “dirty” welding process with lots of smoke and slag.
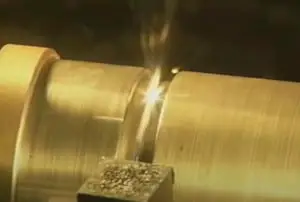
Electron Beam Welders (EBW)
Electron beam welding is a fusion process that joins two metal pieces using a tightly focused beam of high-velocity electrons. The electrons make the two workpieces melt and flow together by transferring kinetic energy in a controlled manner using magnetic fields controlled by computers.
EBW must be done in a vacuum environment. Shielding gas cannot be used, since it can cause the electrons to scatter. Most electron beam welders have a stationary weld gun or head, and computer-controlled machines move the work pieces accurately to weld them.
The benefits of electron beam welding include very high weld strength, highly consistent welds and small heat-affected zone which allows for very precise welds on thin or small work pieces.
The downsides of electron beam welding are the extremely high cost and complexity, and lack of suitability for standard welding applications outside of manufacturing.
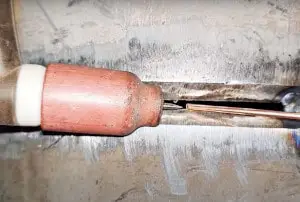
Atomic Hydrogen Welders (AHW)
AHW is an arc welding process that uses two tungsten electrodes. The weld area is shielded by hydrogen gas. When the arc forms between the two electrodes, it superheats the hydrogen gas to 6000-10,000 C. This breaks apart the H2 molecules into individual hydrogen H+ atoms. When these atoms hit the much colder welding surfaces they recombine into H2 again, releasing extremely high heat levels (3000-4000 C).
The main benefit of atomic hydrogen welding is that the tremendous amount of heat released by AHW welders can melt some of the most hardened metals on earth. AHW can weld tungsten, nickel and molybdenum effectively. This makes it ideal for repairing machine tools and other hardened metal objects.
The downsides of atomic hydrogen welding are it’s very dangerous (hydrogen gas is explosive), very costly, can only weld in the flat position, requires high voltage AC power (300 volts plus) and requires a significant amount of training. AHW is not suitable for most general welding applications. For these reasons AHW has been almost completely replaced by TIG welding in the marketplace.
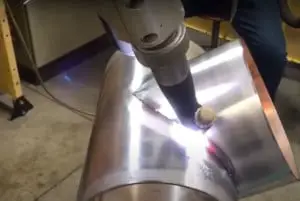
Plasma Arc Welders (PAW)
Plasma arc welding is similar to TIG (GTAW) welding. It uses plasma to transport the electric arc from a tungsten electrode to the metal work piece. The main difference between plasma arc welding and TIG welding is that the plasma arc can be separated from the shielding gas envelope allowing it to reach a very high temperature (up to 20,000 C). This high temperature fuses the two pieces of metal together without filler material.
The benefits of plasma arc welders are that they are very suitable for detailed and precise welding on small or thin pieces. PAW welders are generally used in aviation, medical equipment manufacturing and other industries where precision is essential.
The downsides of plasma arc welding are the very high cost, and unsuitability for joining standard metal pieces like steel bars, pipes or aluminum frames together.
What Kind of Welder Do You Need?
Now let’s cover what each kind of welder does best (and worst), and the 7 different factors to consider before buying one.
If you’re just looking to buy your first welder for repairs and fabrication work, here’s a good beginner’s guide to pick your first welder.
Factor #1: Cost
Cost is always a factor in the decision about what kind of welder you need. Welding machines can cost anywhere from $100 to over $100,000. You also need to consider the cost of consumables such as electrodes and shielding gas, and the supporting hardware required to operate and transport your welder.
From a cost standpoint, here’s how the different types of welders stack up:
Welder Type | Relative Cost | Cost Range |
Flux-Cored Arc MIG (FCAW) | Low | $100-2,000 |
Gas Metal Arc MIG (GMAW) | Medium | $200-3,000 |
Shielded Metal Arc Stick (SMAW) | Low | $100-2,000 |
Gas Tungsten Arc TIG (GTAW) | Medium | $500-5,000 |
Atomic Hydrogen (AHW) | Medium | ??? (out of production) |
Plasma Arc (PAW) | High | $7,000-12,000 |
Electron Beam (EBW) | Very High | $98,000-3,000,000 |
Factor #2: Variety of Metals You Can Weld
Welder Type | Metal Types | Thickness Range |
Flux-Cored Arc MIG (FCAW) | carbon steel, stainless steel, cast iron, aluminum-nickel alloy | 20 GA to 1/4 inch |
Gas Metal Arc MIG (GMAW) | carbon steel, stainless steel, aluminum, magnesium, copper, nickel, silicon bronze, other alloy types | 22 GA to 1/4 inch |
Shielded Metal Arc Stick (SMAW) | carbon steel, stainless steel, alloy steel, cast iron, ductile iron | 10 GA to 1 inch |
Gas Tungsten Arc TIG (GTAW) | carbon steel, stainless steel, chromoly, aluminum, nickel alloys, magnesium, copper, brass, bronze, silver, gold | 26 GA to 1/2 inch |
Atomic Hydrogen (AHW) | tungsten, nickel, molybdenum, chromoly | NA |
Plasma Arc (PAW) | carbon steel, stainless steel, chromoly, aluminum, nickel alloys, magnesium, copper, brass, bronze, silver, gold, cast iron, lead, titanium | 10 GA to 5/16 inch (0 GA) |
Electron Beam (EBW) | carbon steel, stainless steel, chromoly, aluminum, nickel alloys, magnesium, copper, brass, bronze, silver, gold, cast iron, aluminum-lithium alloys, titanium, dissimilar materials (e.g. stainless steel to aluminum alloys) | 0.1 mm to 500 mm |
Factor #3: Welding Positions
Depending on whether your welding is done in a controlled manufacturing environment or outdoors in uncontrolled conditions you will need to consider the welder machine’s ability to weld in different positions.
Welder Type | Welding Positions |
Flux-Cored Arc MIG (FCAW) | flat, horizontal, vertical, overhead |
Gas Metal Arc MIG (GMAW) | flat, horizontal, vertical, overhead |
Shielded Metal Arc Stick (SMAW) | flat, horizontal, vertical, overhead |
Gas Tungsten Arc TIG (GTAW) | flat, horizontal, vertical, overhead |
Atomic Hydrogen (AHW) | flat only |
Plasma Arc (PAW) | flat, horizontal, vertical, overhead |
Electron Beam (EBW) | flat, horizontal, vertical, overhead |
Factor #4: Training Required
Here is the amount of training required to create high quality welds for each type of welder:
Welder Type | Required Training |
Flux-Cored Arc MIG (FCAW) | low |
Gas Metal Arc MIG (GMAW) | medium |
Shielded Metal Arc Stick (SMAW) | medium |
Gas Tungsten Arc TIG (GTAW) | high |
Atomic Hydrogen (AHW) | high |
Plasma Arc (PAW) | high |
Electron Beam (EBW) | high |
Factor #5: Portability
Below is the level of portability for each kind of welder:
Welder Type | Portability |
Flux-Cored Arc MIG (FCAW) | high |
Gas Metal Arc MIG (GMAW) | medium |
Shielded Metal Arc Stick (SMAW) | high |
Gas Tungsten Arc TIG (GTAW) | medium |
Atomic Hydrogen (AHW) | medium |
Plasma Arc (PAW) | low |
Electron Beam (EBW) | low |
Factor #6: Flexibility
Flexibility refers to the ability to use a welder in a variety of different situations, on different types of welds, with different metals and thicknesses. Below is the relative operational flexibility of each type of welder.
Welder Type | Flexibility | Reasons |
Flux-Cored Arc MIG (FCAW) | high | Works in most conditions and applications, highly portable, excellent for production manufacturing |
Gas Metal Arc MIG (GMAW) | medium | Works on a wide variety of metals and thicknesses, does not work outdoors in wind, not very portable |
Shielded Metal Arc Stick (SMAW) | medium | Works outdoors and most metal types, highly portable, does not work on thin metal, not good for production manufacturing because it’s slow (must change electrodes often) |
Gas Tungsten Arc TIG (GTAW) | medium | Works on a wide variety of metals and thicknesses, does not work outdoors in wind, not very portable |
Atomic Hydrogen (AHW) | low | Only welds in horizontal position in a controlled environment |
Plasma Arc (PAW) | low | Large stationary machine |
Electron Beam (EBW) | low | Large stationary machine |
Factor #7: Welding Speed
The speed you can weld is very important in a production manufacturing or construction environment. It is less important for metal repairs, general fabrication work, automotive and hobby uses. Below are the relative welding speeds by type of welder.
Welder Type | Speed | Reasons |
Flux-Cored Arc MIG (FCAW) | high | Constant automatic feed of flux cored wire allows continuous welding without changing gas |
Gas Metal Arc MIG (GMAW) | medium | Automatic feed of metal wire allows continuous welding, but gas must be replenished |
Shielded Metal Arc Stick (SMAW) | low | Consumable electrode sticks must be changed often, approximately 50% of the welding speed of MIG |
Gas Tungsten Arc TIG (GTAW) | low | Consumable filler sticks must be changed often and the operator must manually control the electrode, weld puddle and arc |
Atomic Hydrogen (AHW) | low | Specialized method requiring significant care and heat control |
Plasma Arc (PAW) | high | Electronically controlled machine automatically manages the arc and moves the welder and work pieces |
Electron Beam (EBW) | high | Electronically controlled machine automatically manages the arc and moves the welder and work pieces |
Pick the Right Welder
In this article we provided tangible information to help you answer the question “What kind of welder do I need?” By understanding the types and uses of different welders, and applying the 7 selection factors above, you should be able to pick the right type welder for your specific requirements.