Are you planning to get your first welder and are still deciding between a MIG or stick?
In this article we discuss how MIG and stick welding compare across 6 factors. This should help pick the right machine for you.
MIG vs Stick Comparison Factors to Consider
- Ease of Use
- Materials
- Weld Quality
- Weld Speed
- Cost
- Safety
Keep reading to learn how these factors compare between the two types of welders.
Basics of MIG and Stick Welding
How a MIG Welder Works
MIG is the acronym for Metal Inert Gas; it’s also referred to as GMAW (Gas Metal Arc Welding) according to the American welding society.
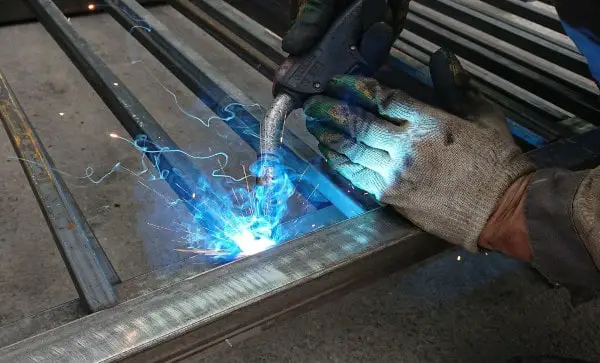
MIG welders have a handheld gun that automatically feeds consumable electrode wire from a spool through a long cable connected to the main machine. The piece that is being welded (or any metal it’s clamped to) is grounded with a clamp. When the welder presses the trigger it charges the wire electrode and feeds the wire at a fixed rate through the tip of the gun.
The MIG welding method uses inert gas to shield the molten weld puddle from the atmosphere. This shielding gas flows through the cable and out of a shielding tip that surrounds the wire electrode when the trigger is pressed. The gas is contained in a bottle with a regulator that feeds into the machine and down the cable to the gun. If you run out of shielding gas a MIG welder will start popping and create poor quality welds.
The inert shielding gas is usually a mixture of CO2 and Argon for typical mild steel welding. For some applications where high heat is required such as copper, magnesium alloy or aluminum it’s better to use helium.
With a MIG welder the electric arc heats up the base metal and melts the continuously fed electrode wire into the molten base metal to join pieces together. The shielding gas protects the molten puddle from oxidization until it cools down and solidifies.
You can learn more about MIG welding in our “how MIG works” article here.
How a Stick Welder Works
Stick welding is the oldest welding method. It is an arc welding method that uses a consumable electrode stick instead of a feed-through wire.
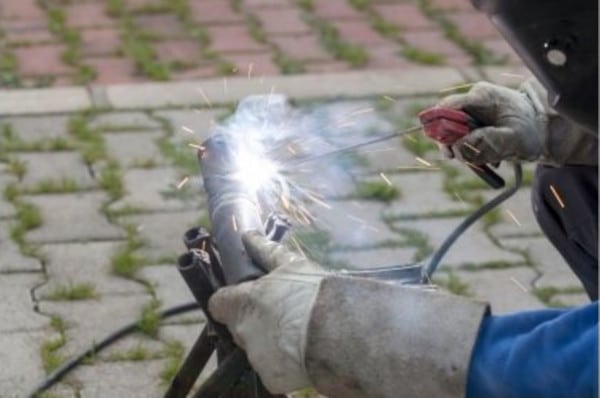
The electrode stick has a covering around it called flux. This flux covering vaporizes as the arc melts the metal electrode in the center of the stick. Heating the flux releases inert gas, which shields the weld puddle from the atmosphere similar to the inert gas in a MIG welder. The shielding flux creates a layer of brittle slag on the weld that you have to chip off after you weld.
The stick is held in a clamp which is held in the welder’s hand. The welder controls the stick directly as he or she welds the work pieces. As the electrode stick melts and forms a weld bead, it is consumed and becomes progressively shorter until it needs to be replaced.
With a stick welder, just like a MIG welder, the work piece (or metal object it’s connected to) is grounded with a clamp to complete the electric arc circuit from the welding machine.
With a stick welder you must choose the right electrode stick to match the metal you are welding. There are many different lengths and types of sticks available.
For either 220 volt MIG or stick welding you will need to have a properly installed 50 amp plug and wiring.
MIG vs. Stick Welding: Ease of Use
Controlling the Welder
MIG welding is considered better than stick welding for beginners because it takes much of the guesswork out of creating a decent weld. All you have to do is feed the wire through the gun, turn on the shielding gas, hit the trigger and it will lay down a spot or bead weld.
Most modern MIG welders have easy-to-use knobs to adjust amperage and wire speed. All you need to do is look on the table that comes with your machine, match up the amps and wire speed with the type and thickness of metal you’re welding, and the settings will be in the ballpark. Once you’ve got your baseline settings OK with a MIG welder, you can focus on perfecting the distance and angle of the electrode tip from your work, and the weld pattern you make with the gun.
In comparison, a stick welder requires you “strike an arc” accurately, and to constantly adjust for the ever-shorter electrode stick. It can be difficult to maintain contact with the work piece to keep the arc going and make a long bead. It takes lots of practice to lay down consistent welds with a stick welder.
With a stick welder, getting to the right settings requires more trial and error. First you need to select the right electrode stick type and thickness, then the right amperage. Then you may need to experiment a bit to get the machine “in the zone”.
Weld Visibility
A key thing that makes stick welding difficult are the smoke, sparks, spatter and slag that come off the weld. This makes the weld pool much more difficult to see compared to a MIG welder.
Greater weld pool visibility means it’s easier to lay down a more accurate weld with a MIG compared to a stick welder. For beginners, the less dramatic it is the easier the machine is to use.
Mobility
One of the downsides of MIG welding is that the cable between the gun and the machine limits your mobility. When you’re working around a vehicle or structure it can be annoying to have to move the base machine. The gun may not want to go where you want it to without adjusting your body or the welder. Stick welders have a lot more freedom of movement.
Finally, MIG welding uses a separate gas cylinder, which requires a wheeled stand. The combination of machine, gas cylinder and stand are heavy and difficult to move around. And replacing or refilling a gas cylinder when you run out isn’t as simple as changing out electrodes on a stick welder. Stick welders are simpler and lighter, and therefore more mobile.
MIG vs. Stick Welding: Materials
A MIG welder is ideal for different metals with varying thicknesses. MIG can weld mild steel, iron, stainless steel, chromoly, aluminum and alloy mixes. You just change to different gas mixes and wire type to adapt to different metals. This makes MIG welders very flexible.
Stick welders to an excellent job with steel or iron, and they can weld stainless steel, but they should not be used with metals such as aluminum that require high heat and oxidize easily.
Stick welders also do a good job of welding dirty and rusty surfaces. As the flux vaporizes and expands from around the weld pool, it does a good job of taking impurities with it. This makes stick welders ideal for outdoor construction, fencing, oil field, ship building and farm equipment work.
You can weld thinner metal with a MIG, since the machine amperage and wire speed can be turned down in fine increments. In comparison, stick welding tends to blow through thin metal and create messy splatter that requires careful grinding and sanding to remove without taking off too much of the base metal. The smoke from the flux burning off also makes detail work on thin metal difficult with a stick welder.
Stick welding is great for thicker metals like heavy plate, thick pipe and rebar. The machine size needed to get good weld penetration is smaller than a MIG machine, and the cost of electrode sticks is significantly lower than specialized large-diameter wire plus gas. If you regularly weld steel thicker than 1/4 inch then stick welding is your best bet.
MIG vs. Stick Welding: Weld Quality
Weld Appearance
MIG welding is far better than stick welding when it comes to the aesthetics of the weld. Stick welding leaves a layer of slag that needs to be chipped off. It also generates a lot of spatter around the weld area — these small molten dots of metal need to be ground or sanded off if you care about having a smooth surface.
MIG delivers a clean and professional looking weld, even if you have moderate experience. However, MIG welding can have similar aesthetic problems if you fail to clean the weld area of corrosion or paint beforehand.
Weld Penetration & Strength
Weld penetration and strength are complex topics that have as much to do with your machine settings and technique as whether you are doing MIG or stick welding.
Generally speaking, it is easier to get full weld penetration with a stick welder. This is especially true outdoors when it’s windy — the flux vaporizes and creates a gas shield that expands away from the weld pool. MIG shielding gas can easily blow away in the wind. Improper gas shielding will create porosity and inconsistent penetration, leading to a weak weld.
This excellent video compares the weld quality from a multi-mode Lincoln MP210 welder that can do MIG with gas, flux cored MIG and stick (arc) welding:
When welded properly on the right settings with the right amps and consumables, there is no substantial difference in weld quality between a MIG and stick welder.
As long as your welding environment is controlled, your technique is good, and the material you’re welding has been cleaned and prepped properly, you will get the same weld strength from a MIG welder or stick welder.
MIG vs. Stick Welding: Weld Speed
One of the major benefits of a MIG machine is how fast it can lay down a quality weld. MIG welding is roughly twice as fast as stick welding.
There are two reasons for this:
- A stick welder electrode and flux takes longer to melt, fill the weld puddle and achieve full penetration. A MIG welder does not have to expend energy heating flux, so all of the heat can be used to melt the wire and base metal and keep the weld puddle flowing.
- The wire feed of a MIG welder quickly and continuously delivers material into the weld puddle for as long as you hold the trigger down. So you can stay welding on the work piece longer with MIG. There is no stopping to change electrodes like a stick welder.
Depending on the material and stick you’re using, you can expect to change stick welding electrodes every 4-6 inches of weld. That compares with NO stopping a MIG weld at all (unless the machine maxes out its duty cycle and you need to let it cool down).
If you need high productivity then a MIG machine is clearly superior to a stick machine.
MIG vs. Stick Welding: Cost
There are significant cost differences between MIG and stick welding.
Welding Machine Cost
MIG welders are typically more expensive than stick welders for the same quality and capacity. Here we compare the approximate cost of three MIG machines and three stick welders with 180 amp capacity (enough to weld 1/4 inch plate) , you can see that stick welding machines are about 20% cheaper.
MIG Welder | Cost | Stick Welder | Cost |
LINCOLN ELECTRIC K2698-1 Easy MIG 180 | $860-880 | ESAB 0700500070 MINIARC Rogue ES 180i | $780-800 |
Eastwood MIG 180 Welder | $600-650 | Forney 235 AC/DC Stick Welder | $500-550 |
YESWELDER Digital MIG-205DS | $450-480 | Eastwood ARC200i Inverter Stick Welder | $390-400 |
Keep in mind also that you will need to purchase a wheeled stand to hold your MIG welder and gas cylinder. This is an additional cost not required for stick welding.
Consumables Cost
MIG and stick welding differ fundamentally on the type of consumables required. MIG requires a gas bottle that needs to be periodically refilled, a roll of wire and gun nozzle tips (cheap). Stick welding requires only electrodes which you purchase by the box.
To compare the cost of consumables you need to calculate the cost per pound of weld. The table below roughly compares the cost of MIG vs. stick welding consumables.
In our estimate it costs $14.24 per pound of weld for MIG welding and $8.97 per pound of weld for stick welding. This does not include the cost of labor, which is higher for stick welding because it takes more time.
Welding Method | Consumable | Cost / Pound of Weld |
MIG | 5 cubic feet of Argon / CO2 mix gas (PRICE = $2.00 per cubic foot) | $10.00 |
0.030″ (0.8 mm) wire – Lincoln Electric SuperArc L-56 ER70S-6 (PRICE = $53 per 12.5 lb spool) | $4.24 | |
TOTAL | $14.24 | |
Stick | 1/8″ (3.175 mm) 7018 mild steel stick electrode – Lincoln Electric Excalibur 7018 XMR (PRICE = $175 for 3 x 10 pound cans). About 65% of the electrode weight is deposited as weld while 35% burns off. | $8.97 |
MIG vs. Stick Welding: Safety
Welding Burn Risk
MIG welding is a generally cleaner process than stick welding, with less smoke, sparks and molten metal spatter to contend with. There is less likelihood of getting burned or lighting your environment on fire while MIG welding. This makes MIG safer than stick welding when it comes to burn risk.
Inhalation of Welding Smoke and Fumes
Smoke inhalation is another factor — MIG emits a smaller amount of fumes and is generally safer than stick welding when done indoors.
Any flux-coated electrode, be it stick or flux wire MIG, will generate a lot of caustic smoke. You should avoid inhaling these fumes as much as possible, and ensure your environment is well-ventilated. Wearing a helmet-mounted respirator pack is a tremendously good idea!
According to the American Welding Society the plume of stick welding fumes can be extremely toxic, depending on what you’re welding and how much you are exposed.
Here are some of the known risks of inhaling welding fumes:
- Burning eyes and skin
- Dizziness
- Nausea
- Fever
- Siderosis (iron deposits in your lungs)
- Manganese poisoning (affects your nervous system)
- Cancer (from calcium or nickel in some metals like stainless steel)
- Cadmium poisoning (cadmium is used as a metal coating and exposure can kill you in 20 minutes or less)
- Ozone poisoning (welding arcs in argon shielding gas or the nitrogen in normal air release ozone, which cannot be seen, smelled or filtered out with a respirator)
You can find more information on welding safety and hazardous smoke and fumes in this OSHA pamphlet https://www.osha.gov/sites/default/files/publications/OSHA_FS-3647_Welding.pdf
MIG Welding vs Stick Welding: Which Is Best?
The choice of MIG or stick welding comes down to your specific situation and intended use. However, looking at the 6 factors we compared above, here is our verdict:
Factor | Winner |
Ease of Use | MIG |
Materials | MIG |
Weld Quality | MIG |
Weld Speed | MIG |
Cost | Stick |
Safety | MIG |
OVERALL WINNER | MIG |
THE VERDICT: MIG welding is the clear winner over stick welding. Stick welding is better for outdoor use and heavy ferrous materials. It costs less and is more mobile. But MIG clearly outperforms stick welding in most situations.